Guides CGR
Application
Tout savoir sur la mesure et les capteurs de pression
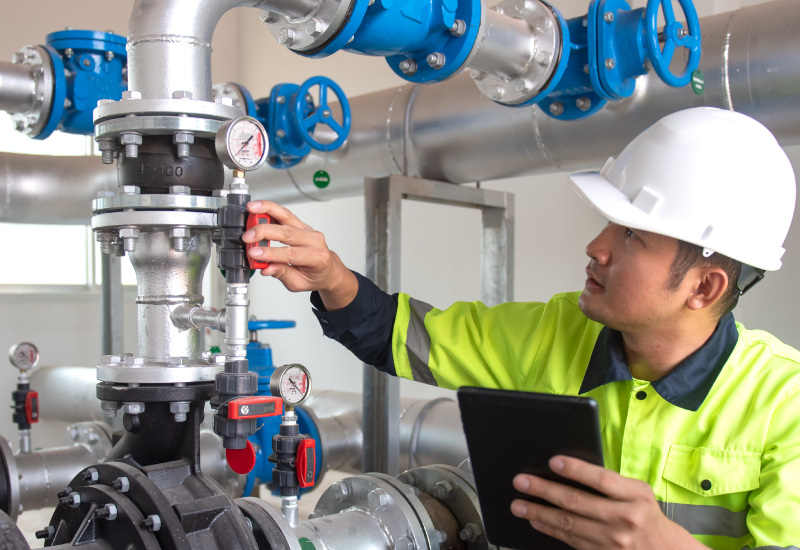
La mesure de la pression joue un rôle crucial dans divers domaines tels que l'industrie et les secteurs du chauffage, de la ventilation et de la climatisation (CVC). Il est essentiel de pouvoir détecter, mesurer et surveiller la pression dans les circuits hydrauliques ou gazeux afin de maintenir le contrôle et d'éviter tous les risques de surpression ou de dépression susceptibles d'endommager les équipements.
Bien comprendre la pression
La pression (P) est une force (F) appliquée sur une surface spécifique (S), exprimée par la formule P = F/S. Dans le système international, l'unité de mesure de la pression est le Pascal (Pa). Elle correspond à une force de 1 Newton (N) agissant sur une surface de 1 mètre carré (m²). L'unité usuelle pour mesurer la pression des fluides est le bar, où 1 bar équivaut à 100 kiloPascals (kPa).
Les différents types de pression
Pression atmosphérique
C'est la force exercée par le poids de l'air qui nous entoure sur une surface donnée. Au niveau de la mer, elle est d'environ 1 013 hPa, soit 1.013 bar ou 1 013 mbar. La pression atmosphérique varie en fonction de la météo, de la localisation géographique et de l'altitude. Elle est plus élevée au niveau de la mer et plus basse en haute montagne.
Pression relative
C'est la mesure de la pression, lue aux manomètres, dans les systèmes de tuyauterie. Elle peut être positive (surpression) ou négative (dépression) et ne tient pas compte de la pression atmosphérique. Elle est exprimée en pascals (Pa) ou bars (bar) selon l'appareil de mesure utilisé.
Pression absolue
Elle est mesurée par rapport au vide absolu, sans aucune pression environnante. Elle correspond à la différence entre la pression mesurée et le vide absolu. Elle est égale à la pression relative additionnée à la pression atmosphérique (Pabs = Prel + Patm).
Pression différentielle
Elle indique la différence de pression entre deux points distincts mesurée au même instant (ΔP = P1 - P2). Elle est utilisée pour surveiller le colmatage des filtres, détecter des niveaux d'eau ou pour mesurer des débits.
Pourquoi mesurer la pression des installations ?
Dans les installations standards, la mesure de la pression relative suffit pour :
- Assurer leur bon fonctionnement ;
- Optimiser les performances des équipements ;
- Contrôler les processus comme la distillation ou la filtration ;
- Diagnostiquer d'éventuels dysfonctionnements.
Dans des applications plus spécifiques impliquant des liquides, vapeur ou gaz dangereux, il peut être nécessaire de tenir compte des variations de la pression atmosphérique. Dans ces cas-là, il est impératif d'utiliser des appareils adaptés pour mesurer la pression absolue.
Les différents appareils pour mesurer la pression
Pour effectuer des mesures de pression (relative, absolue ou différentielle), on utilise couramment deux types d'appareils : les manomètres et les capteurs de pression.
Les manomètres
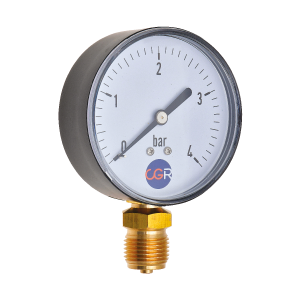
Les manomètres sont des appareils mécaniques composés d'un élément sensible qui se déforme sous l'effet de la pression. On distingue 4 types de manomètres :
Manomètre à tube bourdon ou à tube manométrique
La pression du fluide déforme un tube ce qui entraîne la rotation de l'aiguille par l'intermédiaire d'une biellette. Il s'agit du manomètre le plus couramment utilisé dans les systèmes de tuyauterie.
Manomètre à membrane (ou à diaphragme)
La pression du fluide déforme une membrane circulaire maintenue entre deux brides, ce qui fait tourner l'aiguille via une tige de transmission.
Manomètre à capsule
Il est constitué de deux membranes circulaires hermétiques assemblées sur leur circonférence. Le fluide déforme la capsule, qui agit proportionnellement sur le mécanisme de lecture.
Manomètre à soufflet
La pression déforme le soufflet dans sa longueur, mettant ainsi en mouvement l'aiguille.
Ces quatre types de manomètres existent en version "pression absolue" pour pouvoir mesurer des pressions indépendamment de la pression atmosphérique. La pression du fluide est mesurée contre la pression de référence, soit le vide absolu.
Il existe des manomètres digitaux. Ils se distinguent des manomètres mécaniques par leur précision.
Les capteurs de pression
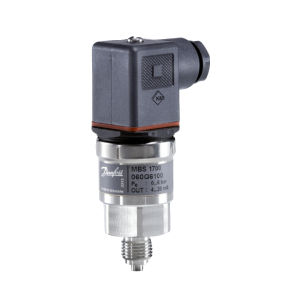
Les capteurs de pression sont des dispositifs électroniques équipés d'une cellule de mesure en contact avec le fluide. Ils convertissent la pression physique en un signal électrique (4.20 mA ou 0-10 V DC). Ce signal peut être lu directement sur un afficheur ou être envoyé vers un automate, un régulateur ou un système de gestion de données.
Étant dépourvus de pièces mobiles, ces capteurs sont insensibles aux coups de bélier, ce qui leur confère fiabilité, précision et durabilité. Ils sont de plus en plus utilisés dans l'automatisation des processus industriels.
L'étalonnage
Dans certaines applications industrielles, il est essentiel de procéder à un étalonnage périodique des appareils de mesure pour assurer la fiabilité des relevés de pression. L'étalonnage implique de comparer l'appareil avec un instrument de référence appelé "étalon". Pour garantir l'exactitude des relevés, l'étalon lui-même doit être préalablement étalonné par un organisme de certification agréé.
Nos conseils pour installer des appareils de mesure de pression
Une bonne installation des appareils de mesure de pression est impérative. Voici quelques conseils :
- Vérifiez que l'appareil est compatible avec les conditions de service telles que le fluide, la pression et la température.
- Choisissez un emplacement sécurisé. Pour éviter les chocs accidentels, les fortes vibrations ou les températures ambiantes excessives, il est possible de déporter le manomètre en installant un capillaire. Si le manomètre est exposé à de faibles vibrations, l'utilisation d'un manomètre à bain d'huile est recommandée.
- Installez des siphons pour protéger les manomètres des fluides à températures élevées. Ils permettent d'abaisser la température d'environ 30% à l'entrée de l'appareil.
- Sélectionnez le type de montage (axial, radial) approprié et assurez-vous de l'étanchéité.
- Utilisez l'outillage adapté lors du montage pour ne pas exercer de contrainte sur l'instrument.
- Lors de la mise en service de l'installation, veillez à ouvrir les différents robinets et vannes progressivement pour éviter les coups de bélier et les chocs thermiques qui pourraient affecter les appareils de mesure.
- Surveillez régulièrement les appareils pour détecter et prévenir les risques de défaillances tels que :
- des oscillations rapides de l'aiguille du manomètre qui pourraient entraîner une usure prématurée de l'appareil ;
- des vibrations qui risquent de détériorer le mécanisme ;
- des surpressions qui entraînent une mise en butée de l'aiguille et provoquer la rupture du mécanisme.
Des questions ? Notre équipe commerciale est à votre disposition pour vous aider à déterminer le produit idéal pour votre projet. Retrouvez sur notre site une gamme complète d'outils de mesure proposée par les plus grands fabricants.
Ces guides pourraient vous intéresser
Souhaitez-vous installer un raccourci CGR-Robinetterie sur votre mobile?